浸滲劑是以硅酸鈉為主要原料,添加無機金屬鹽、穩定劑、表面劑和懸浮劑等組成。它具有 、易清洗、耐熱等許多優點;且填充能力大、分散性能好;該系列浸滲劑貯存穩定、保質期長、使用方便、且低廉。適合于鑄鐵、鑄鋼、鋁合金、合金等各種金屬受壓鑄件的泄漏滲補。由于該系列浸滲劑具有以上許多優點,浸滲處理后的產品儲存時間長,只要鑄件金屬組織自身不腐蝕,被堵的微孔處是不會腐蝕的。由于SH是一種穩定的化合物,即使金屬組織自身被腐蝕,堵漏部份化合物仍維持原狀。
浸滲工藝流程:
浸滲設備在壓鑄件及粉末冶金件制造過程中,由于氣體殘留、晶體收縮等原因,不可避免地形成大量微孔、砂眼、裂紋,微孔滲漏給機器設備的使用帶來隱患,即使用于無壓力要求的用途也可能因電鍍,涂漆及其它表面處理時電鍍液,酸液等進入零件內部導致內部腐蝕,縮短了零件使用壽命,因微孔的存在使表面噴漆、電鍍等形成氣泡或凹凸不平。
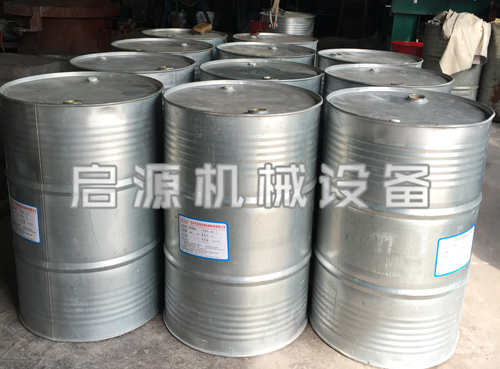
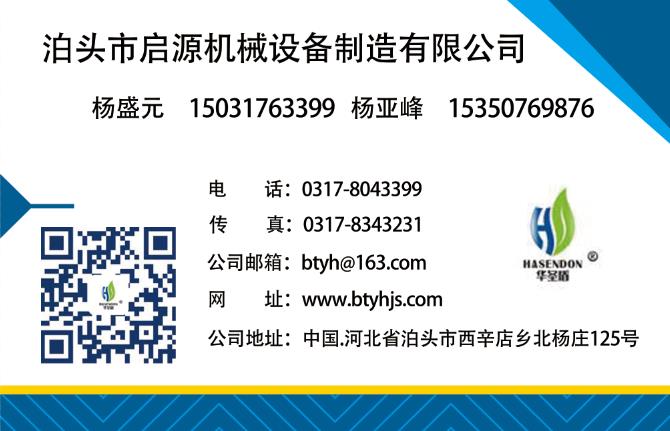
<一>、浸滲工藝的發展
浸滲工藝的目的是利用浸滲劑在壓力下滲入到多孔性產品零件中去,然后經固化聚合反應,以達到填充空隙、密封堵漏和承壓的要求。
浸滲設備浸滲工藝廣泛用于鑄造缺點的,木材的防蟲、防腐、阻燃,粉末冶金件的增強和密封,水泥制品的防酸堿腐蝕,電器、電了元件的防潮和絕緣。
近代工業浸滲工藝的應用可以追溯到上世紀三十年代的鑄件堵漏工藝,當時用水玻璃以內循環填充鑄件空隙。
上世紀五六十年代,隨著汽車工業的發展,美國、前聯邦德國為承壓鑄件的密封推動了前一代浸滲劑一一硅酸鈉型浸滲劑的研制和應用,并由局部或常壓浸滲工藝發展到真空加壓浸滲工藝。
上世紀七十年代以來,汽車向輕型化發展,許多鑄件被鋁、鎂、鋅等輕金屬及其合金材料所代替,從而減輕了汽車重量,減少了能源消耗,提高了汽車的使用性能。
但輕金屬鑄件容易產生微孔,導致受壓鑄件滲漏,同時,粉末冶金燒結件的廣泛應用,進一步節省了材料和機械加工費用。
多孔材料急待解決的泄漏問題,對浸滲技術的需求。
同時化學工業的發展,又浸滲劑的研究與開發。
種類繁多,用途廣泛,性能優良的浸滲劑不斷出現,相繼推出了聚酷型二代浸滲劑和厭氧型、熱固性丙烯酸酷型第三代浸滲劑。
浸滲方法和浸滲工藝不斷得到改進,浸滲設備向大型化、半白動化方向發展,進一步推動了浸滲工藝的廣泛應用,推動了許多復雜結構件設計的薄壁化。
現在一些企業已把浸滲工藝作為鑄件生產中不可缺少的生產工序,并主張對鑄件進行浸滲全處理。
<二>、浸滲工藝流程和浸滲方法
1用無機硅酸鈉(水玻璃)浸滲劑浸滲
采用無機硅酸鈉(水玻璃)浸滲劑浸滲的工藝流程。
工藝步驟:加工裝配好閥門,封閉閥門2端法蘭,微開啟閥門密封面(閘板密封圈不接觸閥座密封面),向閥門體腔注入模數為1.5~2.0的無機硅酸鈉(水玻璃)浸滲劑,注入的浸滲劑液面高于密封圈上沿即可,關閉浸滲劑輸入閥,用空壓機給閥門體腔加壓0.4一0.6MPa保持壓力15min后,將閥門體腔卸壓至零(恢復到常壓),回收閥門體腔內浸滲劑放入浸滲劑儲罐,向閥門體腔內吹入二碳氣體(3~5min)可使浸滲劑固化,從而大大縮短浸滲時間(或常溫下將浸滲過的閥門放置20~26h,讓浸滲劑自然固化),打開閥門,清理粘結在閥門體腔及銅合金密封圈表面的浸滲劑固化后的殘余物(殘余物有一定的粘結力和強度,需要借助工具清理),浸滲完成。按閥門壓力試驗要求對閥門進行壓力試驗。試驗時,如還有因材料微空引起的滲漏,可以重復上述浸滲過程,直至閥門壓力試驗合格。
2用有機甲基丙烯酸脂浸滲劑浸滲
工藝步驟:加工裝配好閥門,用除脂劑對閥門體腔及銅合金密封圈進行除脂處理,對除脂后的閥門體腔及銅合金密封圈用清水沖洗2~3min,用空壓機吹干閥門體腔及銅合金密封圈表面的水,封閉閥門兩端法蘭,微開啟閥門密封面(閘板密封圈不接觸閥座密封面),用真空泵將閥門體腔抽真空(-0.1MPa)并保壓15min向閥門體腔注入有機甲基丙烯酸脂浸滲劑,注入的浸滲劑液面高于密封圈上沿即可,關閉浸滲劑輸入閥,再用真空泵將閥門體腔抽真空(-0.1MPa)并保壓15min左右,將閥門體腔恢復常壓至零位,用空壓機給閥門體腔加壓0.4~0.6MPa保持壓力15min后,再將閥門體腔卸壓至零位,回收閥門體腔內浸滲劑放入浸滲劑儲罐,打開閥門,用清水沖洗閥門體腔及銅合金密封圈表面3~5min給閥門體腔注入90℃~95℃的熱水并保持20min進行固化,或將電熱吹風機固定在一個能移動的小支架上,對銅密封圈(浸滲表面)加熱(90℃~95℃,450W電熱吹風機口距工件表面250~270mm)30min進行浸滲固化,浸滲完成。按閥門壓力試驗要求對閥門進行壓力試驗。
泊頭市啟源機械設備制造有限公司(http://www.btyhjs.com)從事無機浸滲設備、有機浸滲設備、氣孔微孔浸滲處理產品已浸透到華北、西北、華南、東北的鑄造行業,深受到業內專家的好評,用戶的親睞。