浸滲技術是解決鑄件泄漏的措施。它是通過真空加壓的方法,使浸滲劑滲入鑄件疏松、氣孔等缺點內部,經過固化、填充鑄件微孔,從而解決泄漏問題,達到密封承壓的目的。目前浸滲技術應用面不斷擴大,浸滲技術已被汽車、船舶和其它主要工業部門認可和應用。主要用于鑄件補漏和燒結多孔性材料密封,也用于電器元件的絕緣性能提高,塑料組合件的密封,以及工件電鍍,涂飾的前、預處理工序等方面,對提高產品的合格率、節約能源,降低成本有明顯的技術經濟效益。
浸滲設備的分類:
按照使用媒介的區別,分為無機浸滲設備和有機浸滲設備。
無機浸滲設備:使用媒介是硅酸鹽浸滲濟。
有機浸滲設備:使用媒介是有機浸滲劑。按照固化溫度區分為:
85℃熱水固化方式的有機浸滲設備(簡稱YJ85℃)
98℃熱水固化方式的有機浸滲設備(簡稱YJ98B)
110℃以上烘烤固化的有機浸滲設備(簡稱YJ110X)
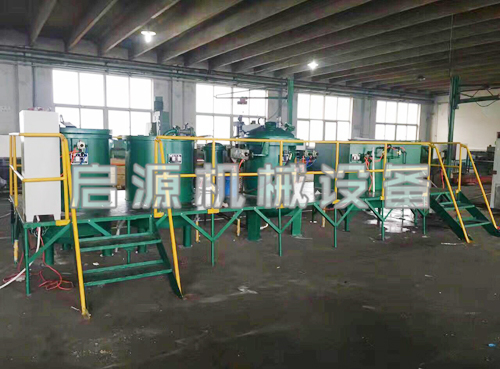
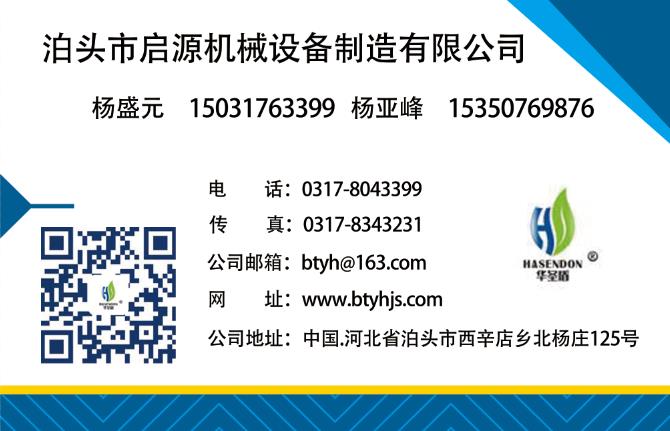
一、鑄造缺點形成原因
金屬零件在鑄造過程中,當液態的熔融金屬開始凝固時,由于內部殘留的各種氣體不能夠完全排出,同時金屬結晶在收縮過程中產生收縮不均,從而造成鑄件內部及表面不可避免的形成氣孔、縮孔、裂紋及疏松等用肉眼難以發現的微孔缺點。
現代汽車工業為了減輕發動機重量、節約油耗,汽車設計過程中較大限度的采用鋁、鎂、鋅等有色輕金屬及其合金材料和薄壁結構鑄件作為發動機設計中的優先選擇,因此現代發動機本體特別是1.6升排量以下的發動機本體的設計發展趨勢為采用鋁合金鑄造技術加工缸體,但由于鋁缸體在鑄造的過程中易出現組織縮松、微孔等鑄造缺點,特別是當代鋁缸體的鑄造均采用了高壓鑄造技術,這種技術對缸體鑄造來說固然是一個質的飛躍(高壓鑄造缸體外表面組織致密,硬度值偏高,加工余量均勻,工件質量有很大改觀),然而鑄造微孔數量比普通的重力鑄造還要多。
這些微孔不均勻的分布在缸體的各個斷面上,從其分布特點看,可以分為點狀氣孔,網狀氣孔及綜合氣孔,從其形態來看可分為封閉孔、盲孔及通孔。
那么高壓鑄造產生微孔的原因是什么呢?經研究證明其原因主要有兩個,一個是鑄件凝固時急劇散熱而收縮產生的收縮孔,另外一個是空氣中的水分與鋁發生反應產生鋁和氫氣,在凝固的時候由于氫氣四處竄而產生氣孔,形成微孔。
微孔的形成是鑄造的機理方面的缺點,其對鑄件的強度不會造成影響,但是由于微孔的存在,會造成鑄件的密封性能喪失,從而變成廢品。
為了彌補這些鑄造缺點,降低生產成本,浸滲設備浸滲工藝技術得到應用和發展。
二、整體真空加壓浸滲工藝
1前處理
(1)清洗先將配有金屬清洗劑的清洗液加熱至40~80℃,然后將裝好的零件吊筐放入清洗機內(零件擺放要易于出水),起動清洗機,使清洗液翻滾,沖洗零件,洗去表面油污等臟物,2~3min停機,對于油污嚴重的宜作多次清洗,然后用清水沖洗干凈。
(2)干燥將清洗后的零件,在60~80℃烘干1h以上,或自然晾干水分。
2浸滲
(1)裝罐將經前處理的零件裝入浸滲罐,密封。
(2)抽真空啟動真空泵,使得浸滲罐內真空度達5.33kPa以上,真空延續時間)15min,停泵,然后打開進液閥門,利用真空負壓將浸滲劑吸入浸滲罐內,并控制浸滲劑液面至超出零件3~5cm高度時關閉進液閥門,停止進液。
(3)加壓關閉浸滲罐通真空泵閥門,打開通空壓機閥門,待恢復常壓后啟動空壓機,加壓至0.5一0.6MPa,保持壓力時間)20min,然后放氣,在壓力降至0.1MPa時,打開貯液罐閥門,利用剩余壓力,使浸滲劑流回貯液罐。
3后處理(水洗)
取出鑄件,在清洗罐清水中洗10s左右,洗去零件表面粘附的浸滲劑。
4固化處理
(1)干燥將零件在室溫(18~25℃)擱置24h以上,晾干水分。
(2)固化將零件放入固化罐,通電加熱到80℃左右,保溫固化2h。如果需要在300℃以上條件使用,再加熱至110℃,保溫固化1h,取出零件,轉試壓檢驗。
泊頭市啟源機械設備制造有限公司(http://www.btyhjs.com)從事無機浸滲設備、有機浸滲設備、氣孔微孔浸滲處理產品已浸透到華北、西北、華南、東北的鑄造行業,深受到業內專家的好評,用戶的親睞。